Indigo Dyeing Process - Indigo and Weld
- Renee Hougey
- Oct 4, 2021
- 4 min read
The problem with my mother vat was a pH imbalance. I WAS going to wait for test strips and do things the "right" way. But I was far too enthusiastic to do nothing on the project for the 2-3 days it would take for test strips to get here. I did a some limited search about medieval dyeing practices.
Somewhere in the 15th century, as clothes got more and more ornate, dyeing became something done by professionals. However, most images of dyeing from earlier periods make it seem like a household task. Would a non-professional dyer have used pH test strips in 1320? Litmus itself was discovered in 1300, and an understanding of pH is only documented since the 1800s. While medieval people certainly understood certain chemicals reacted certain ways, I highly doubt a medieval home dyer would use a pH test, trusting a recipe instead. So I did so.
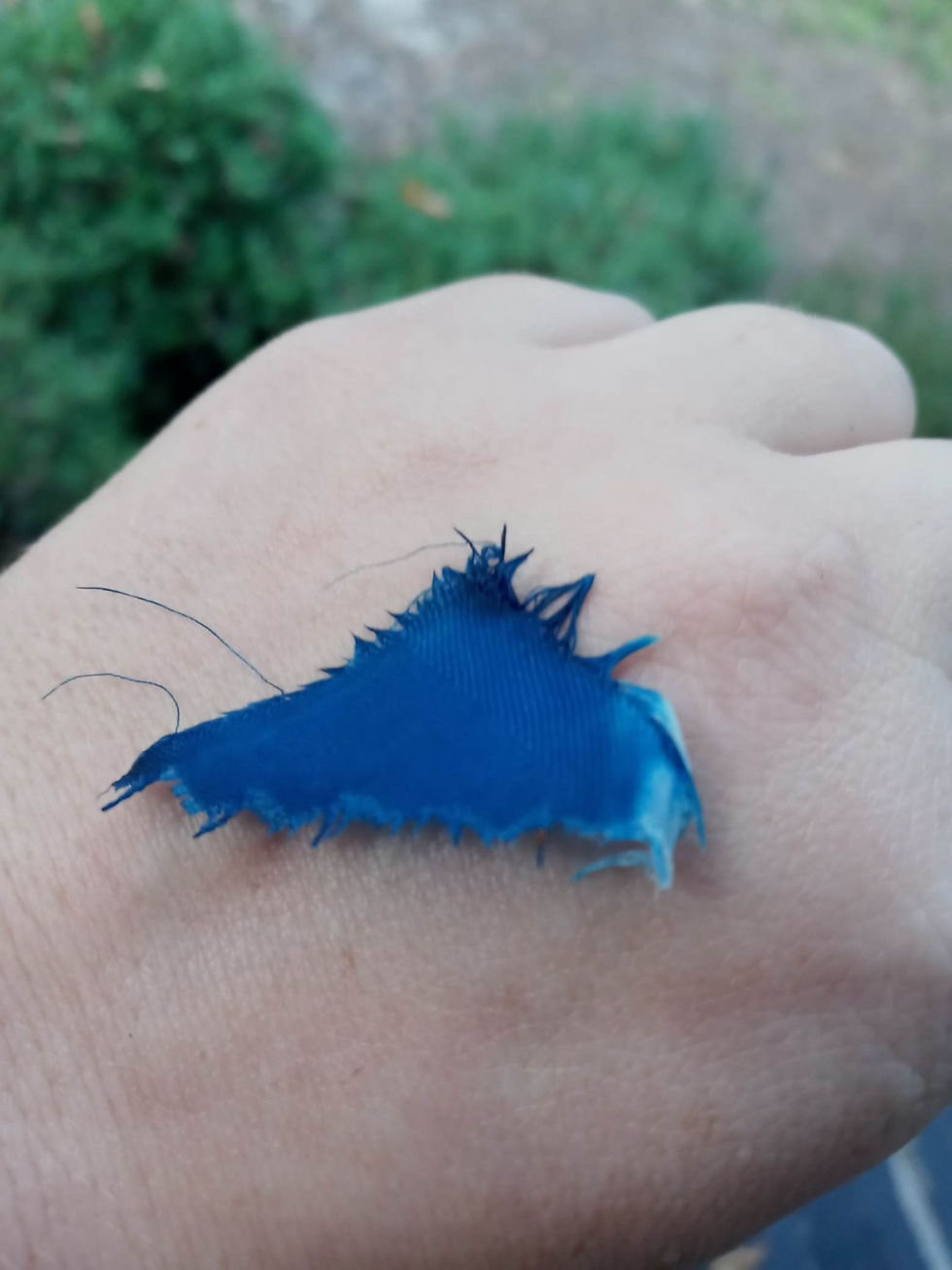
I tested the indigo dye on a scrap, did 3 dips, followed by thorough washing. I got the color I wanted. I proceeded to the full dye vat, with the proportions of the test vat. I was more successful with the Thiox, adding the second half after the flower seemed fully formed. I also added rabbit hide glue, at 2 tsp per pound of fabric (or just under 1 tsp for this fabric, to protect the silk protein fibers from the acidity of the dye. I'd soaked the glue crystals in 12 ounces of cold water for a few hours before adding hot water to make 1 liter of hide glue solution the same temperature as my vat. (Proportions found here: https://www.suzannedekel.com/post/setting-up-a-hydros-indigo-vat )
There was ONE problem - I did not have enough indigo to match the amount of water needed to submerge the cloth (I had enough for 10 liters, but needed closer to 18 liters). I was very, very concerned that the dye would be too weak.
That was an unfounded concern.
The full vat was ready at about 8:30 PM. I wasn't going to be dipping indigo in my kitchen, so I did it on the front porch. In the dark. (I've had better plans.) I figured the lighting would make the fabric appear darker than it was, and knew that the fabric being wet would make it look darker, and had read that I could expect enough dye to wash out as to make the fabric 2-3 shades lighter.
The vat was hot (though at about the 140F/60C all the directions indicated, and dropping as it sat on my porch). I did my best to nudge the "flower" to the side (I had a whole dang BOUQUET - it covered the top of the vat, so this was a difficult proposition.) I gently lowered the fabric in as evenly as possible, and did my best to stir it without disturbing the surface of the water and oxygenating things, with a 3-4 minute dip. I pulled it out, and my husband helped me to stretch the fabric out evenly so that the dye didn't pool or drip. We gently floated the fabric, like kids with those parachutes at school, letting it cool and oxygenate. It did not take long for the fabric to turn very blue. The second dip was about 90-120 seconds (I started counting once the fabric was submerged), with the lighter end of the cloth dipped in first - the color was reasonably even after the second dip). I debated skipping the third dip, as the fabric seemed to be appropriately dark, but I figured the lighting might be messing with me, and I "knew" the big vat wasn't as strong. The third dip was also 90-120 seconds.
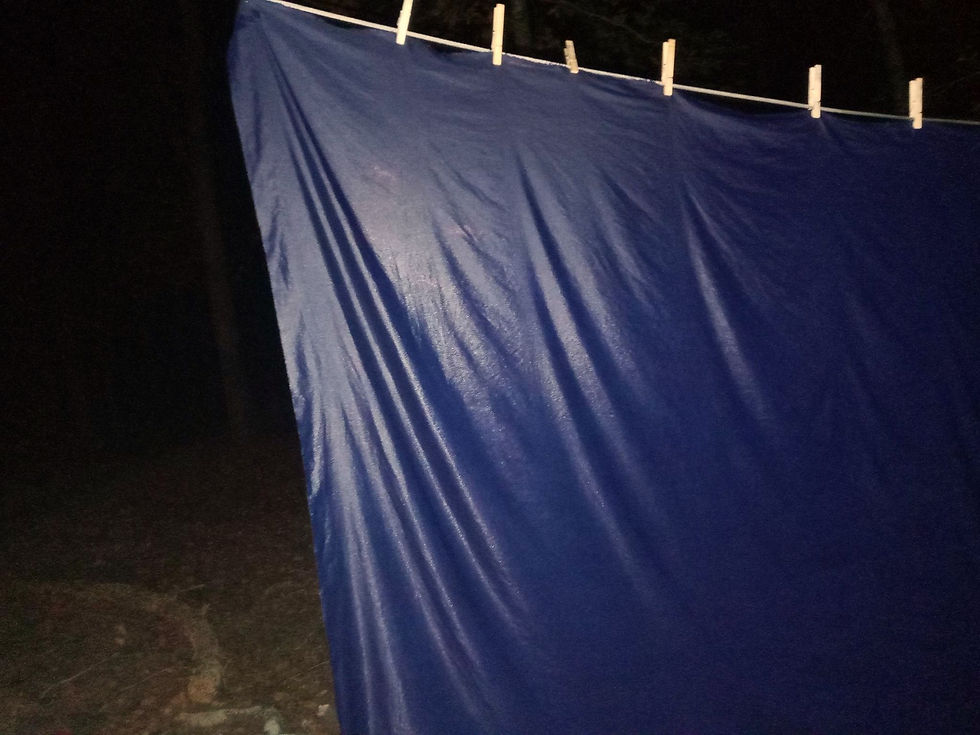
Well. That was darker than expected...
After the third oxidizing, I hung it up to let it dry enough to not drip indigo through the house.
Tried to go to bed. No. Nope. That won't happen. The CLOTH IS OUT THERE.
Retrieved the cloth when it was only mildly damp, and washed it by hand 4 times, in the hottest water that I could, until the suds and water were running clear. It... hadn't... lightened. Oh. Oh dear. This might be a problem. OK, nothing for it. I like dark greens. It will be FINE. At about 1 AM, I put it in the mordant.

That's dark. That's worryingly dark. Not giving up, though. I was following the amalgamated instructions, aside from pH testing, and I was NOT giving up. Fabric in the alum mordant for the night. Maybe more dye will leech out as it soaks.
Next morning, around 10:30 AM, I drain the cloth. The water is absolutely clear. Rinse the pot. Start the weld.
Indigo is picky. Indigo is weird. But if you have ever dyed anything, whether with Rit dyes or procion dyes, you can do weld. I wet my weld powder into a paste, and put it into my 130 degree f pot, filled with enough water to submerge my cloth. Stick the cloth in. Stir regularly and monitor the temperature until it's the right color (90-120 minutes in this case).

Oh, still worryingly dark, but that hue. My green-loving heart be still.
I took the vat off the heat and let it sit for another 45 minutes, because the weld particulate makes it look more yellow than it is (and it's hot). Hung the fabric to dry enough to judge the hue, and....

Oh. Oh my. When that dries... Yes, this will work. I have bought so much fabric that is that color.
So. I left it about 4 hours to dry, took it in again, and gave it 3 thorough washings before I was out of shampoo.
I hung it up again, and sat outside to watch fabric dry. The temperature was perfect. There was a light breeze. I watched the fabric dry and flutter in every shade of my favorite color (dark grass green to deep peacock green, with dark emerald in there too). The fabric lightened just enough...

Ooooooh yeah.

This is the most true to life picture of the final color and variegation. While I intended for the color to be more even, I could not be happier with the results.
As an addendum: I got pH strips and tried to test my vat. Indigo, funny enough, dyed the pH strips, so that kind of makes them wildly invalid anyway.
Comments